The Challenge of Global Sustainment: The Case of the Osprey
As the Osprey is added to the US Navy fleet and to that of Japan, the challenge is growing with regard to global sustainment.
This was our look at the challenge in 2015.
2015-06-14 By Robbin Laird
In September 2007, the Osprey was deployed for the first time to Iraq.
USMC Commandant Conway and Deputy Commandant of Aviation Castellaw announced and made the decision to deploy the Osprey into combat although virtually all public commentators thought this was too early for an “untested” airplane, as one critic put it.
http://sldinfo.com/osprey-at-the-five-year-mark-looking-forward-to-the-future/
Fast forward to 2015 – 8 years of operational engagements – it is hard to believe this is the same plane.
The Marines are now the only tiltrotar-enabled assault force in the world and are reworking their concepts of operations throughout based in large part on the Osprey and its ability to operate from multiple platforms and locations.
The demand for these unique assets is very high with the Marines operating globally in support of US military operations.
The early start in Iraq – with baby steps in operational terms — now sees the plane operating virtually everywhere in the world.
And the USAF with its CV-22s is doing much the same thing.
But the plane was never built as a global product, nor designed neither for global sourcing nor for wide-ranging, high demand global support.
The program has reached a critical turning point – can the Osprey be purchased by allies, supported by a global supply chain and effectively supported worldwide?
Can that allied opportunity be merged with an enhanced capacity to support forward deployed Ospreys, flown by the Marines, the Air Force and soon the Navy for its Carrier support operations?
Put bluntly, the current system of support is falling short of meeting such a growing demand signal. In interviews I have done over the past few years with Osprey maintainers and operators, it is clear that there is a concern with supply shortfalls and uncertainties unduly affecting operational demands. Again, because the demand signal is higher than DoD decision makers expected, the supply side has fallen short.
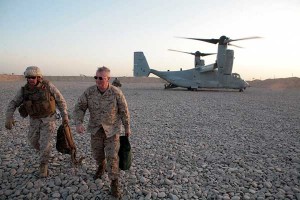
In the words of former USMC Deputy Commandant for Aviation, LtGen Trautman,
“As a growing number of unprecedented new missions and operating locations are added to the V-22 community’s repertoire and new international and domestic customers seek to obtain the Osprey, we must ensure the global supply chain evolves to keep pace with this incredible revolution in military technology.”
In an interview, which I did with Lt. Col. Boniface in early 2014 at New River, the Osprey commander underscored what he saw as a significant problem.
He focused on the critical need to have a responsive and effective parts availability pool to support the deployed but dispersed ARG-MEU.
This is an especially important challenge for the Osprey because of relatively limited locations within which parts are available to be flown or delivered to the ARG-MEU on deployment.
Put another way, the deployment of the ARG-MEU is not constrained by Osprey operations, but the effectiveness of the logistics or sustainment operations.
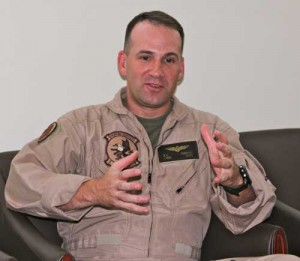
And the exit interview I did with Colonel Christopher ‘Mongo’ Seymour in the Summer of 2013 during the week prior to his retirement, the hard hitting and well-respected Marine Corps leader provided a look back and a way ahead with regard to sustainment of the Osprey.
QUESTION: A major challenge in fielding a new system is getting the supply chain up and working and getting the inevitably maintenance problems sorted out. How have you worked through these problems?
Col. Seymour: There are three separate streams of activity which need to align to really get the new system up and running and integrated into operations.
The first is getting the Marines committed to owning the system and learning how to fix “new” problems, which come up with a new system. The problems are different and have to be worked differently. You need to get the maintainers to change their culture.
Sorting out problems with the gearbox is a good example of what needed to be done. The gearbox on this airplane is very complex and central to its unique operational capabilities. The gearbox inside the nacelle turns a rotor, and they were chipping. This is high-end engineering.
But it was chipping and when it did so maintainers put it aside and waited for a new part. This meant the fleet was going to be degraded.
The flight line needed to take ownership of the problem because a lot of it was self-inflicted gunshot wounds. Maintainers would look to blame someone else when they had a proper gearbox go bad. As it turns out, the, the technology required was ti yse isotropic oil that actually absorbs moisture out of the air, so if you have a gearbox that’s not turning and boiling the oil out on a regular basis, it goes long term down. It’s sucking in the moisture of the North Carolina Coast into the oil.
And the maintainers would leave it out on the flight line all opened up just breathing the air, and then when they finally got a part or piece, they try to fire it up and another gearbox would chip or another problem would manifest itself someplace else. It was an endless loop.
We took some ownership here on flight line, and shaped better maintenance practices, and to help industry.
Once we got that proper gearbox moving back out of the red into the black, the internal culture of the community changed to become significantly more optimistic, you know.
The maintenance man-hours required to change a proper gearbox initially was estimated at 1800 maintenance man-hours.
We’re doing it now in about 380.
That’s how good we got at it.
QUESTION: The first challenge then was simply to get the maintainers familiar with the plane, adjusting their practices and communicating better with industry to solve the gearbox problem. What were the other challenges?
Col. Seymour: The second thread is industry.
The key challenge is to get industry working to solve the right problems, or the critical problems, which would make a difference.
But as we focus on solving a core problem, there is the challenge of dealing with simpler problems, which emerge, which then slip between the cracks.
Once industry is on a steady track, the PBL system incentivizes industry to drive down cost.
They will not do this if they have little capacity to know what our operational costs for a system and its component parts are.
We have to work with industry to get the reliability of key parts up and then the PBL system works quite well to shape an incentive system for industry to deliver parts on time and to improve costs.
The third thread is the government. In our case, the challenge is to get NAVAIR focused on solving the critical problems, and not just dealing with the low hanging fruit.
When we got NAVAIR focused on solving the gearbox problem as the key, industry kicked in and worked the problem as a priority.
The challenge is get those three strands to work together effectively – the USMC, industry and NAVAIR.
[maxgallery id=”76217″]
Seymour in the discussion in New River at the end of June 2013 provided a number of insights into what was necessary to succeed in shaping a new culture for maintenance.
“A key challenge is to let the maintainers are not stakeholders but Marines. For example, I had a gunny sergeant who said he preferred CH-46s to Ospreys.
“He said that I’m a 46 guy.” I looked him in the face and said, “Well, you’re in the wrong unit, gunny. There are no 46 that’s left here on the East Coast. You want me to get your orders to Okinawa, because, you know, that’s the only place for flying 46s.”
I told him that you don’t get a vote. This is not a democracy. Conway decided. McCorkle decided. Hagee decided. Amos decided, you know, we’re going to fly the Osprey. It is what it is, so either embrace it or leave.”
He then underscored where that Gunny is now in terms of working the Osprey.
“The same gunny now will brag about being, , the gunny who fixed problem X, Y, or Z in the maintenance department on a V-22. He owns it now. It’s like okay, you know, it worked, it’s normalized if you will, and that’s why you see this, this growing success. Success begets success internal to the Marine Corps culture.”
Seymour underscored the importance of industry and the SYSCOM listening to the Marines as they deployed the plane.
“We had another problem with the gearbox where it attaches inside in nacelle with a component called the drag pin that, that holds that, that gearbox in place.
There’s a fitting around that drag pin that with vibrational wear and would fall out.
And so you had to pull the whole gearbox out, replace this $25 bushing and put the whole gearbox back in at a cost of like 1800 maintenance man hours initially. So we did a lot of kicking and screaming at industry in and to the SYSCOM.
Are you guys, are you guys kidding us?
You know, you want us to pull this $1 million component out to replace a $25 bushing at the expense of 1800 man hours probably equates to a million dollars just in labor cost, right?
We don’t pay labor cost obviously, but it’s a good argument to make.
Marine labor is free, but it comes on the backs of marines and it’s demoralizing to the community.”
Seymour also underscored the challenges of getting NAVAIR focused on solving critical problems, rather than what was easiest to solve.
“NAVAIR has taken credit on briefing charts for dealing with low-hanging fruit. We have not fixed the gearbox but you got this. You know, what do you do? That’s not going to do anything for me. That gives me, you know, a 0.001 percent bump in readiness.
What’s going to get me a double-digit bump in readiness is having the proper gearbox.
We finally got the SYSCOM focused on the gearbox, which, which actually focused industry on fixing the gearbox. Industry invested a lot of their own money, upfront money when they had to, with the multi-year PBL.
They could not get this gearbox into the PBL because industry saw it as too risky. The costs were all over the chart. They would replace one gearbox or repair one gearbox for $800,000 and repair another one for $50,000. And of course, NAVAIR and NAVSUP wanted a flatline PBL and industry understandably wouldn’t take the risk.”
If you go for the low-hanging fruit, it might make you feel better for 30 seconds, but it’s not going to solve the problem.
Go after the hard, the big-bone items and that’s what this gearbox was.
It was a big-bone item.”
He revisited the PBL issue when asked what is the key item, which needs to be remedied currently.
“Blades, rotor blades, prop rotor blades. It drives me insane because in complexity, that proper gearbox is like splitting the atom and that blade sitting on top of it, it’s like a 2 x 4.
They focused all their energy on fixing the proper gearbox and they took their eye off the blades and, and now we got into this big bathtub on improper blades.
But it is absolutely solvable, and it’s a PBL item.
Industry is incentivized to improve reliability of the blade because every time they got to fix one, it costs them money. So they are going to work hard.
You’ll see probably in the next two or three years the blades won’t be a problem anymore.
But we’re going through this bathtub right now where they just weren’t incentivized to focus on it. They were making more money dealing with the blades when they came in for repairs, but now that it is part of the PBL they will solve it.”
What Seymour focused upon and dedicated many years of efforts to was to get the maintenance and sustainment system moving in the right direction for the USMC.
Now the scope of the challenge is widening: there is a need to embrace global support for global customers and to forward deployed US forces using the Osprey.
But to get a global system in place will not be easy, for the Osprey was not designed from the ground up to be a global system.
This will require shaping what one retired senior Marine Corps leader called a “normative performance based logistics systems.”
And what he means by this is more significant investment by industry and government in the parts sourcing, and better sharing of information and risk in getting a global system in place.
Clearly, a global sourcing system is possible, and Boeing might look no further than their very successful C-17 global sustainment program.
The C-17 has parts sharing and support by the company worldwide and only this sustainment program has allowed allies to buy the airplane and to work completely inter-actively with the US Air Force.
Parts Sharing Among Allies: The Case of the C-17 from SldInfo.com on Vimeo.
As the former head of the RAAF Airlift Group put it in an interview:
The Boeing managed Global Sustainment Program is a C-17 support mechanism that was designed for the United States Air Force, so it can maneuver anywhere around the world. And so, people who have received common training in different units could look after that aircraft as it deployed globally.
As international sales started with Britain and then with Australia with the C-17 in completely different hemispheres of the world, we felt that this agreement still was USAF centric. So if a British C-17 was visiting Australia and had an engine malfunction or something go wrong with it, and needed technical support with more than a couple of technicians it was carrying, Australia could not do anything to it without Britain asking America’s permission to do that work.
That worked for about the first six weeks.
Then we realized that this was obviously a shortfall in our ability to conduct worldwide operations and support.
We now have a totally different approach.
In the GSP we do not own the common spares; our common spares are part of a global C-17 inventory. Any of our air crew or technicians can walk up to any C-17 support area in the world, and actually submit an order form through which looks like a United States document.
And because the partner technicians have gone through the same training processes, they can help fix that malfunction that’s occurred.
This is the gold standard for working a multinational fleet and we see a similar process being established for the F-35 and we would certainly like to see that for the KC-30A as well.
With aircraft that operate globally, you do not want to be limited by the logistics simply being supported by national parts, which may well not be located at the point of attack or in the area of interest. This makes no sense with the multi-national and multi-mission aircraft becoming the norm for 21st century air forces.
Clearly, such an approach needs to be shaped to enable the global opportunity of the Osprey to unfold.
It would be a significant failure if this does not happen simply by failing to meet the strategic shift, which a new approach to Osprey sustainment requires.
The recently announced sale of Ospreys to Japan provides an opportunity to re-shape the approach and put in motion a more global approach.
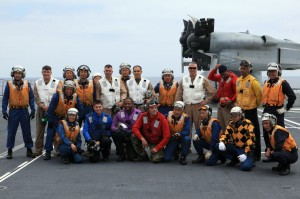
Ospreys operating from Japan and by Japan will operate from a high demand and high stress-operating environment.
CV-22s, MV-22s and Japanese V-22s can all be sourced from a common warehouse with a higher than adequate supply part sourcing.
Because demand is flexible and the US Ospreys operate throughout the region, ramping up parts stores in a regional warehouse would make sense and start the process of globalization of the Osprey on a sound footing.
As Secretary Wynne, the former Principal Deputy Under Secretary of Defense (Acquisition, Technology and Logistics) put it with regard to a major barrier to proper global sourcing:
“It would be important for the Japanese to ensure that they have significant material on their side of the export request for their parts depot.
Marines can guide, but the investment in stock really pays off in terms of operational performance.”