SB>1 Defiant Will Be Worth The Wait: Sikorsky & Boeing
Sikorsky and Boeing are saying that their aircraft is taking longer than Bell’s because their design is more inventive — harder, riskier, and more time-consuming, yes, but ultimately better. In particular, while the SB>1 looks like it’ll be a little slower than the V-280, going by the companies’ projections for top speed, Sikorsky and Boeing say their machine will be much more maneuverable.
Sikorsky and Boeing are painfully aware they’re a year behind archrival Bell in getting their Future Vertical Lift aircraft off the ground. But, the companies insist that when their SB>1 Defiant does take flight, hopefully this December, the Armywill see a revolutionary aircraft, fast and agile, that will be well worth the wait.
“We truly are inventing something here,” said Boeing’s FVL director, Randy Rotte. “The Army wanted… a technological leap, (but) with that great reward there will be challenges, some of which we’ve met and overcome, and some of which are probably still ahead of us.”
So, if ongoing ground testing reveals unexpected problems, I asked, could the first flight slip again, into 2019? Yes, Rotte said bluntly. “(In) the scenario you’ve laid out, which absolutely could happen, (where) we have to do additional work…. and that pushes us out beyond 2018, then we’ll be disappointed, but so be it.”
The Defiant program will not cut corners to go faster, Rotte promised: “We will not let schedule drive us to decisions that we regret.”
World Enough & Time
Even if first flight slips to 2019, Boeing and Sikorsky say, they’ll have plenty of time to get the Army all the test data it needs to make its decision on what to buy. “We’ll give them that data, whether it’s in December or some later date,” said Sikorsky’s FVL director, Rich Koucheravy. (Sikorsky is part of Lockheed Martin).
In fact, the SB>1 Defiant team is already providing data to the Army’s Aviation & Missile Research, Development & Engineering Center, every day. “We have AMRDEC representatives in our daily and weekly meetings,” Koucheravy told me. “We share with them everything that we can.”
So what does the program have to share today? It’s simulations, components on test stands, and a full-scale aircraft “bolted to the ground,” Koucheravy said. This Powertrain System Test Bed (PSTB) lets them run the engines at their full “combined 9,000 shaft horsepower,” he told me, and see how all the components hold up without risking a crash should something fail. What the test bed lacks is landing gear and flight controls — since it can’t go anywhere — and, for the moment, rotor blades.
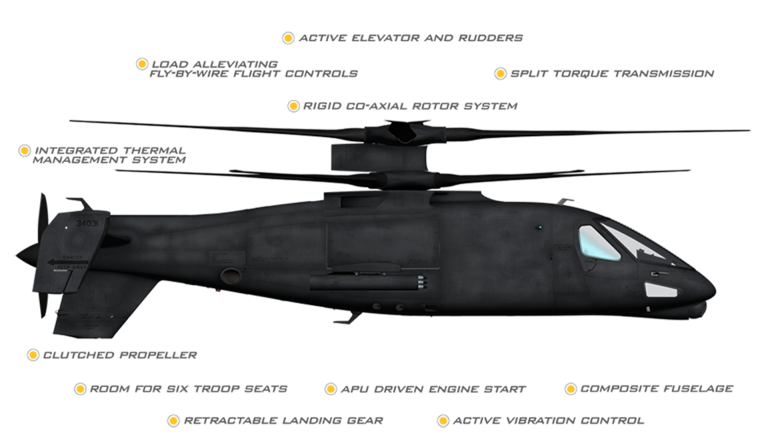
Those rotors have been the biggest holdup for the SB>1. That’s partly because the design requires extremely rigid materials to control vibration, partly because the Army asked Boeing to try out a new manufacturing technique, called automated fiber placement. It would actually have been faster to do this first set of blades by hand, Rotte told me. But while mastering automated manufacturing took longer than planned, he said, it’ll pay off later in more efficient production — that is, if the Army decides to buy SB>1s in bulk. As of now, Rotte said, the first blades are on hand and about to be installed on the static testbed for their first real workout.
The challenge ahead? While Sikorsky’s earlier, smaller X-2 and S-97 Raideraircraft used the same basic design, called a compound helicopter, the SB>1 scales the technology up to an unprecedented size. That means vibration, airflow, and other dynamics may change in ways the models don’t predict.
“This is about a 30,000-pound-plus aircraft,” Koucheravy said. “There has never been a compound helicopter at this size, flying 230, 240, 250 knots and having to maneuver.”
If you boil all their arguments down, Sikorsky and Boeing are saying that their aircraft is taking longer than Bell’s because their design is more inventive — harder, riskier, and more time-consuming, yes, but ultimately better. In particular, while the SB>1 looks like it’ll be a little slower than the V-280, going by the companies’ projections for top speed, Sikorsky and Boeing say their machine will be much more maneuverable. But what makes it so different?
Compound Helicopters Vs. Tiltrotors
The two teams have taken radically different approaches to both designing and publicizing their aircraft. The result to date has been Bell’s utter domination of media coverage. Even before the V-280 took flight for the first time last December— 12 months ahead of the SB>1’s hoped-for first flight — Bell was pouring out photos and videos of the aircraft under construction and in ground testing.
But both Bell and the Sikorsky-Boeing team are trying to solve the same problem. The Pentagon wants to replace the Army’s mainstay UH-60 Black Hawk and similar mid-sized, multi-purpose helicopters with something radically faster and longer-ranged, able to fly through short-lived holes that other weapons blast in advanced Russia or Chinese air defenses.
The Army now calls this the Future Long-Range Assault Aircraft (FLRRA, pronounced “flora”), but earlier names for essentially the same thing are Future Vertical Lift Capability Set 3 (FVL CS-3) and the Joint Multi-Role Technology Demonstrator (JMR TD). Just to complicate matters, after years of prioritizing the mid-sized transport, CS-3 aka FLRRA, the Army announced in March that it also urgently needed a small armed scout, something in FVL Capability Set 1, which became FARA, the Future Armed Reconnaissance Aircraft.
Bell’s approach to all of the above builds on its experience with tiltrotors: aircraft that can take off and land vertically like a helicopter, but tilt their rotors forward to fly with the greater speed and fuel efficiency of a propeller plane. The experimental XV-15 of the 1980s evolved into the V-22 Osprey, a joint venture by Bell and Boeing, which — after a long and painful development, with multiple fatal crashes — is now in wide service with the Marine Corps, Air Force Special Operations, the Navy, and Japan.
The V-22 is big, able to carry 24 fully equipped troops (or a spare F-35 fighter engine). By contrast, the FLRAA will replace the 11-passenger Black Hawk, and the FARA scout must be even smaller, able to hide from radar by flying down city streets. So Bell’s challenge on both aircraft is to scale down its tiltrotor technology. Its advantage is the lessons learned from hundreds of V-22s in service for two decades.
By contrast, the Sikorsky-Boeing team has to scale their technology up, a more difficult problem, with only a handful of experimental aircraft to learn from. Sikorsky started with the award-winning X-2, scaled that up to the S-97 Raider — the leading contender for the FARA scout — and now, with a single functioning S-97 still in flight tests after the first prototype’s “hard landing,” they and Boeing have to scale up again for their FLRAA transport, the SB>1.
Why bother, when we already have big tiltrotors? Because the X2/S-97/SB>1 family are a radically different kind of aircraft. While they look more like a traditional helicopter than tiltrotors do, these compound helicopters are actually a newer and in some ways more advanced technology.
Bell developed the V-22 in the 1990s for the Marines, who fly long distances from Navy ships to targets well inland. So tiltrotor technology emphasizes speed and fuel efficiency, not so much agility — or at least it used to: Bell CEO Mitch Snyder proudly reports a test pilot told him that if the old V-22 flies like a truck, the new V-280 flies like a sports car.
Compound helicopters are probably a little slower than tiltrotors. Bell claims the V-280 will reach a top speed of 280 knots (hence the name), about 322 miles per hour, while Boeing’s Rotte told me the SB>1 is only aiming for 250 knots, the same top speed as Sikorsky’s original X2. (That’s about 287 mph, still much faster than the fastest-ever conventional helicopter, a stripped-down, souped-up Westland Lynx, whose 1986 record of 250 mph has stood for decades).
But compound helicopters might be much more agile at low speeds and in tight quarters — the conditions in which most crashes and shoot-downs occur. When you compare a compound helicopter like the SB>1 Defiant to a traditional helicopter, “not only do you not sacrifice maneuverability,” Boeing’s Rotte told me, “you actually have enhanced maneuverability.”
Why? Because they combine traditional helicopter rotors for vertical lift (albeit a sophisticated low-drag, low-vibration version) with a pusher propeller or “propulsor” for high speed. Low to the ground or in tight quarters, you can use the propulsor to maneuver without tilting the whole aircraft the way a traditional helicopter has to do. Higher up, where you do have room to tilt the whole aircraft, you can use both traditional helicopter maneuvers and the propulsor together to maneuver in ways a conventional helicopter can’t.
“It’s really good to get to the objective area in a combat operation quickly, but if you get there (and) you’re not maneuverable… you’re not survivable,” Sikorsky’s Koucheravy said. With a compound helicopter, “I get in and get out much more quickly, and in the face of enemy fire, I can maneuver, I can turn,” he told me. “The propulsor on this aircraft gives you a new independent power vector that no helicopter has ever had” — and, while he didn’t say so outright, no tiltrotor, either.
Of course, these advantages are mostly theoretical, so far. The sole S-97 Raiderflying is now testing these technologies in real life, albeit in a relatively small aircraft. It’ll be up to the SB>1 Defiant to prove they work at a larger scale — once Sikorsky and Boeing get it in the air.
https://breakingdefense.com/2018/10/sb1-defiant-will-be-worth-the-wait-sikorsky-boeing/