Shaping the Tiltrotor Sustainment Enterprise: Phases of Development
Much like the evolution of the tiltrotor concepts of operations, the tiltrotor sustainment enterprise has gone through its own phases of development.
The evolution of the three variants of the Osprey have gone through three phases of development. The latest tiltrotor variant designed from the ground up for the U.S. Army, takes into account these lessons learned to set in motion an aircraft designed for sustainment in the digital twin age.
The first phase (2007-2014) of Osprey sustainment involved deploying the aircraft for operations in Iraq and Afghanistan. With the deployment began the real-world initial learning and support effort. The operators and the industry field service representatives (FSRs) worked together to support the aircraft in its various missions.
The Osprey is a very different aircraft than either fixed or rotary-wing, and it took time to learn how the operational characteristics affect the aircraft tip to tail in terms of maintainability. Learning about parts performance and shaping a supply chain that delivered parts in a timely fashion was a challenge to be worked.
The second phase (2014-2022) was shaping a regular maintenance regime rhythm. The aircraft is a digital aircraft that provides significant data with regard to its performance. The government worked with industry on performance-based logistics contracts that covered an increasing number of parts to be managed by the Bell-Boeing Original Equipment Manufacturer (OEM).
The third phase (2022-present) has been characterized by engineering redesigns of the aircraft to enable significant improvements in the sustainability of the aircraft leading to higher readiness rates.
As Brad Wanek, Director of V-22 Sustainment at Bell, put it in an interview, “Sustainment improves significantly with the knowledge and experience gained as the service operationalizes the aircraft. Once a level of operational maturity is reached, readiness levels begin to plateau, and it becomes more and more difficult to move the needle. To make significant improvements in readiness thereafter often requires major system improvements and hardware upgrades.”
The first example of this has been the nacelle improvement program, introduced into the USAF fleet of Ospreys starting in 2022. The key objectives of the NI program have been to improve maintainability and reliability, so as to improve the V-22’s mission-capable rate. A reduction in maintenance man-hours to troubleshoot and repair, coupled with reduced failure rate of components results in less downtime and increased mission-capable status.
A second example would be a major modification of the digital infrastructure of the aircraft, in which the computer power would be upgraded allowing for enhanced ability to handle and manage the data for sustaining the aircraft. I will focus on this proposed change in a later article. This would enable other upgrades which rely on processing power and a transition to an open architecture system, as is being designed for the FLRAA.
This phasing is somewhat arbitrary, but it underscores the transition for learning how to sustain a revolutionary aircraft by taking those experiences in understanding how it operates and can be sustained more effectively and regularizing the knowledge and support system.
But one reaches a point where to craft major sustainment improvements on the aircraft, redesign and re-engineering of the aircraft is needed. This process of redesign and re-engineering is aided in part by the launch of the design process for the next aircraft in the tiltrotor enterprise, the FLRAA.
Phase One: Initial Operations and Learning how to Sustain a New Type of Aircraft
Standing up the Osprey in 2007 was a pioneer project. It was sent to Iraq and performed well in its first missions and was supported by the initial supply and maintenance approaches.
I first dealt with Osprey maintainers during a visit to USMC Air Station New River in August 2010. It was here that I began to understand that this was essentially the first digital aircraft that was generating data to aid in establishing a data-drive information support process to shape a more effective maintenance regime going forward.
A sense of the early days was provided by maintainers interviewed during that visit. An interview conducted during that visit provides insight into the challenges being faced in this first phase as perceived at that time.
Question: What has been the challenge of moving from rotorcraft to a tiltrotor craft?
Sergeant Fante: “It was slow, really slow at first because mostly with lack of experience and lack of supply assets.
“Whereas, with the 46 and the 53, we see a part come in and if you didn’t know what it was, you can easily go to QA (Quality Assurance), go to a senior guy to get help. Until we get a part in, everybody is kind of scratching their heads.
“We have to call a civilian an FSR, field service representative and they’d have to come in and kind of guide us along.
“The service vendors provided the transition, because we had no experienced Gunnys. The FSs here and they’re very, very, very adequate.
“They’re awesome guys but before with the traditional aircraft we relied on the long experience of Gunnys.
“And you have enough to pull in assets where you’re going to have parts and you have 30 year’s experience producing parts so there’s going to be a supply chain that’s got capability built into it.”
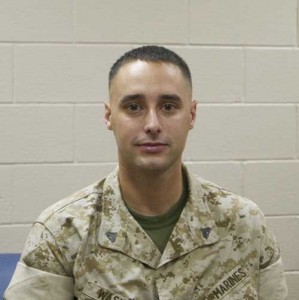
Comment: Whereas, in the case of the Osprey, the supply chain is new and you have challenges with availability of parts and metrics of performance and life cycle of those parts? So you’re either going to have to adjust the metrics to make them realistic and you’re certainly going to have to improve the product towards whatever the “normal” is.
That gets you back to your lack of experience issue. There’s no gunny to go to and say, okay, we’re going to work in sync for a long time, you know, I’m looking at this part, is this normal, right?
It’s hard to have a normal, when you don’t have normal.
Sergeant Fante: “We are dealing with a lot of new recognition issues with regard to the parts and their performance.”
Corporal Warshek: “There is the problem of dealing with changing capabilities. Certain pieces of gear change almost constantly as upgrades are made. This meant we had to learn to adjust.
“For example, we just recently got in first two pendulum assemblies into our shop. We’ve never seen before. We rely on the FSR’s to provide guidance on how we would tackle something like that. The pendulum assembly attaches to the rotor head.”
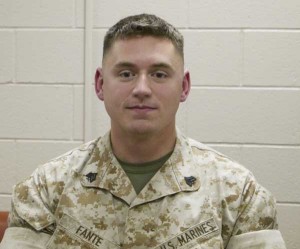
Question: What was your experience in Afghanistan with regard to maintenance?
Corporal Warshek:” I deployed with 261, VMM-261 when they went out.
“Occasionally, we’d run in something like where would be in a situation where the service representative wasn’t available or, we’d be on our own and the publications we were relying on was a little unclear or none of us had seen the problem before quite in the same way. So we would draw upon the “Osprey Nation.”
A key challenge to effectiveness in maintaining the aircraft was the learning curve faced by the maintainers themselves.
I discussed the challenge of enhancing the knowledge and skill of the maintainers to take the sustainment enterprise forward in 2013 with Colonel Chris “Mongo” Seymour at his office in New River.
In a meeting I had with him during his last week of service at New River before retirement in 2013, he noted: “There are several streams of activity which need to align to get the new system up and running and integrated into operations. He spoke in detail about one which was getting the Marines committed to owning the system and learning how to fix “new” problems, which come up with a new system. The challenges are different and must be worked differently. You need to get the maintainers to change their culture.
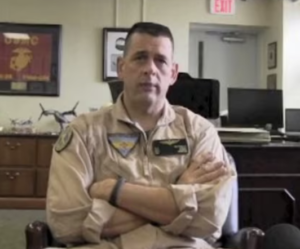
“Sorting out problems with the gearbox is a good example of what needed to be done. The gearbox on this airplane is very complex and central to its unique operational capabilities. The gearbox inside the nacelle turns a rotor, and they were chipping. This is high-end engineering. But when it was chipping, maintainers put it aside and waited for a new part. This meant the fleet was going to be degraded.
“The flight line needed to take ownership of the problem because a lot of it was self-inflicted. Maintainers would look to blame someone else when they had a proprotor gearbox go bad. As it turns out, the technology required was to use Hygroscopic oil that absorbs moisture out of the air, so if you have a gearbox that’s not turning and boiling the water out on a regular basis, it goes long term down because of corrosion. It’s sucking in the moisture of the North Carolina Coast into the oil.”
Phase Two (2014-2022): Shaping a Regular Maintenance Regime Rhythm
As the maintenance practices became standardized, a Performance-Based Logistics System (PBL) set of contracts could be put in place which could more effectively manage the parts for the aircraft.
Defense Acquisition University defines a PBL as follows:
Effective PBL contracts contain core attributes necessary to deliver improved reliability and availability performance at lower cost. These core attributes include:
- A Performance Work Statement (PWS) that clearly defines the needed reliability and availability outcomes and value to the Department to achieve product support outcomes in unambiguous, objective and measurable terms
- The minimal set of metrics that directly support the stated outcomes, are specific enough to hold providers accountable, and do not inhibit or constrain the provider from achieving greater efficiency, cost control, incentivized productivity, and productive processes
- Incentives to deliver performance and reduce total cost
- A baseline and sufficient performance and cost insight to understand the price, cost, and “should cost.”
- An understanding of the risks associated with non-performance and the strategies to mitigate adverse outcomes.
To leverage PBL’s proven ability to deliver needed reliability and availability to DoD customers at reduced cost, the DoD has a goal of ensuring the effective use of PBL, with particular focus on business arrangements that provide financial incentives to industry.
The Osprey has seen several PBLs to date. Over time these PBLs have included more parts to be managed by the OEM but the Osprey has never had a tip-to-tail PBL which limits the ability of the OEM to manage the aircraft
Daniel Devereaux, the PBL program manager at Bell, in a recent interview identified the PBL path in terms of the inclusion of parts covered by these contracts. “The supply chain side of the PBL started in 2012. Currently, there are around 1000 depot level repairables right now: we have 228 of them. The government works with us on the 228 but goes directly to the vendors for the parts they make for the remainder.”
With the U.S. Navy buying its variant of the Osprey and declaring IOC in 2022, an important stimulant to further change in the sustainment enterprise was provided.
I discussed this dynamic in the Fall of 2022 with “Mongo”, now with Bell and then head of sustainment for the Osprey at the company.
Recently, I turned to “Mongo” again to discuss the challenges and opportunities posed by the U.S. Navy now buying into the Osprey capabilities to support the carrier and the fleet. He is now in charge of sustainment at Bell, and we picked back up from our earlier interview.
He highlighted that while the Marines have significant experience in sustaining the aircraft, the Navy has its own learning curve, just as did the Marines earlier.
“It is sort of a ‘ground-hog-day.’ The Navy maintainers are generationally detached from the innovations of the past two decades of Marine Corps operations and development. But they are inheriting more than 20 years of operational experience and are building from that forward with specific U.S. Navy operational demands associated with the large deck carrier and then with the fleet.”
He pointed out that the Navy’s acquisition of the Osprey meant the Navy was taking ownership of the aircraft and making it a naval aircraft instead of a unique Marine Corps platform.
Seymour pointed out that both services benefit from Navy ownership of the platform; the Marines will benefit from Naval ownership and the focus on support from the naval enterprise, while the Navy will benefit from the established global sustainment capabilities and parts distribution points supporting USMC operations.
With regard to the third phase of the Osprey sustainment enterprise, namely re-engineering and redesign for enhanced sustainability I have discussed the key example of such an approach being implemented in terms of the USAF variant of the aircraft, namely, my discussion of the nacelle improvement program with David Albin of Bell.
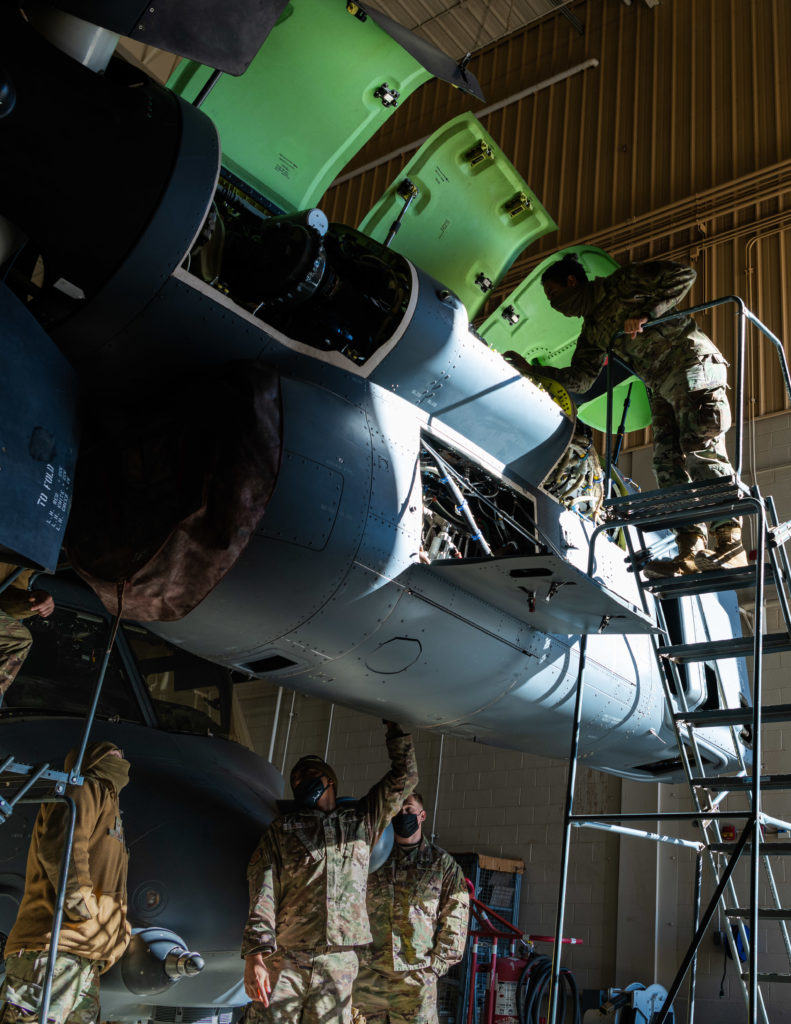
And I will discuss the envisaged redesign of the digital infrastructure of the aircraft in a future article.
But there is little question that the re-engineering and redesign under way for the Osprey can significantly enhance readiness rates, and that the Army-Bell partnership designing a new member of the tiltrotor enterprise clearly builds on and enhances this effort.
Featured Image: Aircraft maintenance contractors utilize a FlexDecks Osprey Wing and Nose Stand to maintain a MV-22B Osprey at Marine Corps Air Station Futenma, Okinawa, Japan, November 28, 2017. The platforms offer full nose and wing fall protection and enhanced worker safety while creating a more proficient maintenance process. It provides the maintainers more accessibility to the aircraft, which ultimately reduces the amount of time the maintainers take to get the aircraft back into the fight. Featuring a compact footprint and high-strength, lightweight aluminum and steel construction, the platform exceeds workplace safety requirements. The Osprey belongs to Marine Medium Tiltrotor Squadron 262, Marine Aircraft Group 36, 1st Marine Aircraft Wing. (U.S. Marine Corps photo by Cpl. Andy Martinez)