The Build-Out of the CH-53K: A Conversation with Paul Lemmo, President of Sikorsky
When I visited NAVAIR at Pax River Naval Air Station earlier this year, I had a chance to meet with the H-53 Heavy Lift Helicopters Program Manager (PMA-261), Colonel Kate Fleeger. She noted that: “The decision to move to Full Rate Production, from my perspective, was a vote of confidence both by the Marine Corps, of course, and the US Navy acquisition chain concerning the readiness of the 53K to transition as planned into the Marine Corps.
“The program of record is for 200 aircraft. We are currently in the 10s to low teens per year build rate. After that we will ramp up to the 20s per year capacity. We currently have nine aircraft already out in the fleet in two different squadrons. One squadron is the operational test squadron, VMX-1, at New River. The second is HMH-461 which is part of MAG-29 at New River, which is the first operational squadron. In addition to the seven aircraft already at HMH-461, we expect them to receive two more aircraft this spring and summer with a total of four to six aircraft by the end of the year.
“The plan is for HMH-461 to be fully transitioned to the CH-53K by the end of next year and be ready for a MEU deployment in 2025. We are focused on this effort.”
I had a chance to follow up on this interview with a visit to the Sikorsky plant in Stratford, Connecticut on 9 May 2023. I began my visit with a conversation with Paul Lemmo, President of Sikorsky, whom I had met many years ago when he was working on maritime programs of various sorts, including Aegis. We met, but this time to talk about a new combat helicopter, the CH-53K.
We started by discussing a key issue raised by Col Fleeger, the focus on full-rate production and the challenge to do so with a taut supply chain. According to Lemmo, the company was on track for the full-rate production build but that the general challenge facing the industrial sector, including defense, with regard to supply chains was an uphill battle, but one which they were focused on and resolving.
And in Lemmo’s perspective, the supply chain effort had to focus not just on the build of the current projected run of aircraft, but on a robust inventory of spares for the maintainability of the CH-53Ks going into the first combat squadron. As Lemmo put it: “We are working closely with the USMC to get sustainment right for the first deployment. We are well on our way to doing that. We are currently sizing our production facility for 24 aircraft per year. And we have baked a number of spares per year into our production capacity.”
The Department of Defense in the long draw down after the Cold War significantly reduced the number of prime contractors and with that saw those primes become more design and assembly houses than full service and production facilities. This meant that the primes outsourced many of the parts and even subsystems to suppliers, thus relying heavily on efficiencies built into a predictable and effective supply chain but designed for just-in time support for wars of choice, not necessity.
Then along came the pandemic followed by the need to upsurge capability due to the Ukraine War and the rising conflict temperature in the Pacific, but the supply chain had not changed for the better. This has meant that Sikorsky in common with other primes has been dealing with the challenge to revitalize and re-energize the supply base.
Lemmo underscored that they can meet their commitments and are focused on finding ways to expand their production capacity in the wake of a rising demand which could come from either additional international or U.S. joint service customers.
As Lemmo characterized the effort: “Lockheed Martin has put about $200 million into this program alone to get ready to build 24 aircraft per year. That is what we will need to do for the USMC program and at least one international customer. Should we be successful with multiple international customers or other joint customers then we will bump that up to 30 or so per year. We will have 12 on the line at any one time and add two lines to the one operating right now.”
We then discussed the supply chain issue and its impact. According to Lemmo: “Every supplier is a different story. We have had challenges associated with raw material or with regard to some suppliers just losing the recipe because they either shed people or they left, and the challenge then is to train the new people to build to the quality levels we need. We are seeing a trajectory in the right direction, but there is definitely more to do in this regard.”
Lemmo did point out that Sikorsky has kept quite a lot of supply work in house. They did this even more significantly in the years of building the Blackhawk and will look closely at second sourcing as they move forward with the CH-53K in which Sikorsky itself could be the second source.
For example, he underscored that “the common thread across all of our platforms are all the dynamic systems, the gearboxes, the rotor systems, the blades, and we do all those in house.”
Later in the day, I visited the production line and discussed the digital maintenance approach with a former Marine I interviewed with Murielle Delaporte many years ago in the Pentagon and who has worked for Sikorsky on CH-53E and CH-53K maintenance approaches and programs, Pierre Garant.
But during the meeting with Lemmo, he provided an overview to the digital backbone approach for designing, building, upgrading, sustaining, and maintaining the CH-53K. Lemmo explained: “The CH-53K is an all-digital aircraft. Both the aircraft and everything on it are digital, and it’s a fly by wire aircraft. The design process was done through model-based system engineering design. And we’ve extended that process out to the production line.
“We build a 53K very differently from a Blackhawk. We use automated tools. The CAD system is on everybody’s tablet working on the aircraft. They’re not trying to look at a piece of paper and figure out what does this really mean; rather they are using digital tools to build the aircraft.
“We’ve extended it out to sustainment as well, so that our operators in the field, whether they be Marine Corps, or our field service reps, have the whole model on their tablet, and they can troubleshoot things much more quickly as well as to reach back for help.
“All that’s added up to an improved learning curve. Traditionally, Black Hawk is around 93%. And what we’re seeing on the CH-53K is below 90%. The lower the number on the learning curve, it means you’re learning quicker. Through digitization, we’re seeing the learning on the 20th helicopter we build similar to what we have not seen until the 100th helicopter on legacy programs. So that’s a big difference.”
We then moved to a discussion about the era of warfighting in which the CH-53K is being birthed. It is an era in which the focus is upon force distribution to enhance the survivability of the force. But as one PACFLEET logistics specialist noted to me recently: “As the operational force is distributed to increase survivability, it exacerbates the sustainment problem. That is a real challenge. And we have bought and are buying a force structure based on legacy concepts of logistics efficiency and not really for effectiveness across a broader area of operations over which a force will distribute.”
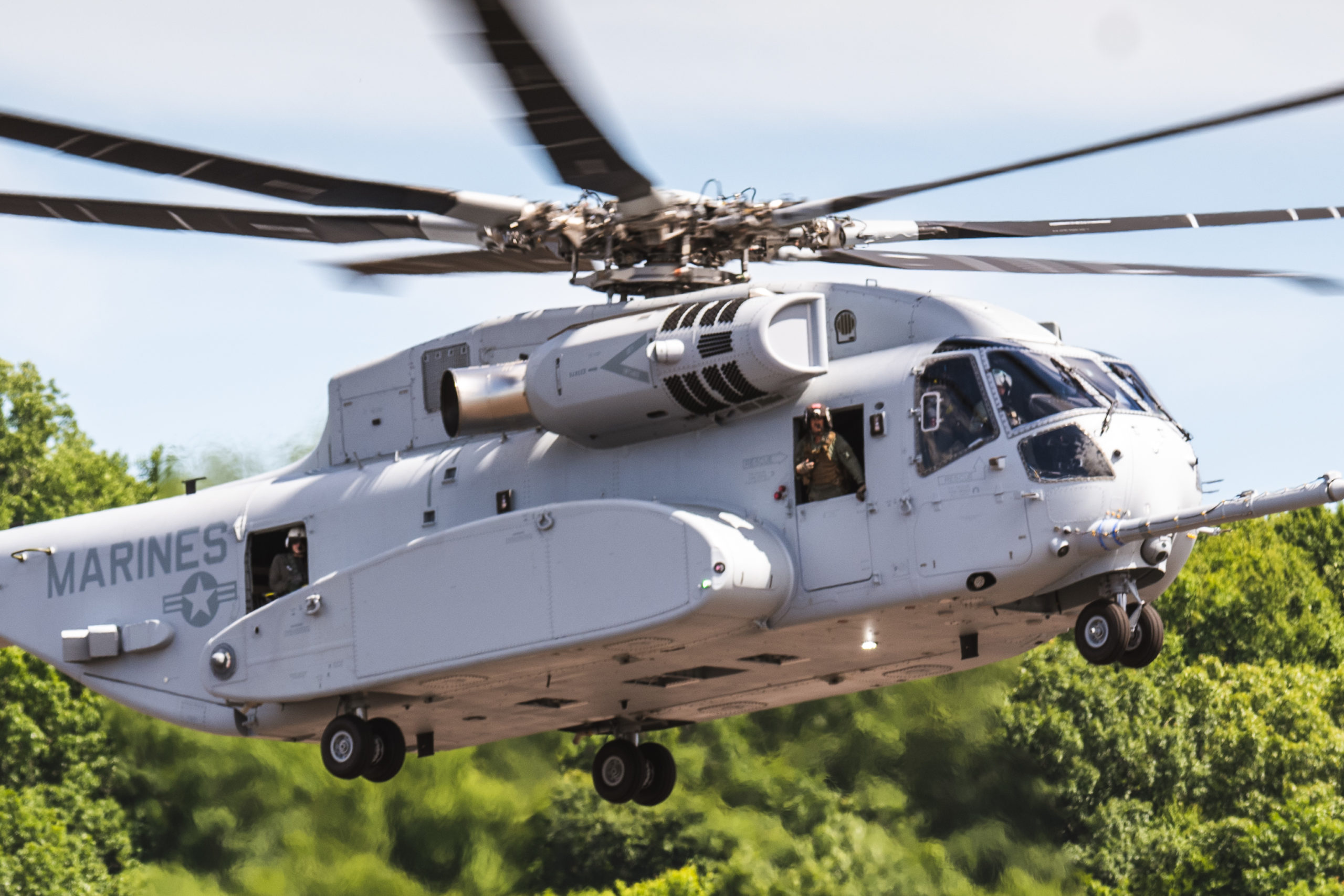
It is clear that the Navy has a serious challenge in being able to do intra-theater logistics in contested conditions as opposed to sending supplies from hubs with a point A to B focus, not in contested situations. As a senior Admiral underscored to me during my recent trip to Honolulu: “If we are going to have distributed maritime operations, we better have the ability to support, battle damage repair, sustainment, and medical services provided at way more rapid than 20 knots.”
The USAF in the Pacific is focused on agile combat employment and a PACAF officer underscored to me the huge challenge which is facing the force to support an Agile Combat Employment or ACE deployed force in a crisis. He stated: “I believe that agile combat employment for the Air Force is a prerequisite to anything else we do. Because if we don’t come up with a way to preserve our combat fighting ability, so we can actually use it, then it will have no value.”
All this means is that the logistics and sustainment threads in the joint force are critical strategic capabilities going forward. Why would not the unique capabilities of the CH-53K make them valuable platforms to contribute to meeting this challenge?
Lemmo noted that the “CH-53K is a game changer because of how much you load onto it, how much you lift externally, how you can operate it, and how it can work with other platforms in the combat space. It is very efficient in terms of cost per ton of what you can deliver to a distributed location.”
And with significant innovation underway with regard to the payloads you can take on board a lift aircraft, there will be developments with regard to how the users will leverage the aircraft. As Lemmo highlighted: “We have only begun to explore what the CH-53K could do. As concepts of operations evolve, the aircraft will evolve with them.”
In short, the CH-53K is a unique platform from a platform point of view. But even more significantly, it is coming to the force at a time of significant change on the con-ops being shaped to employ that force.